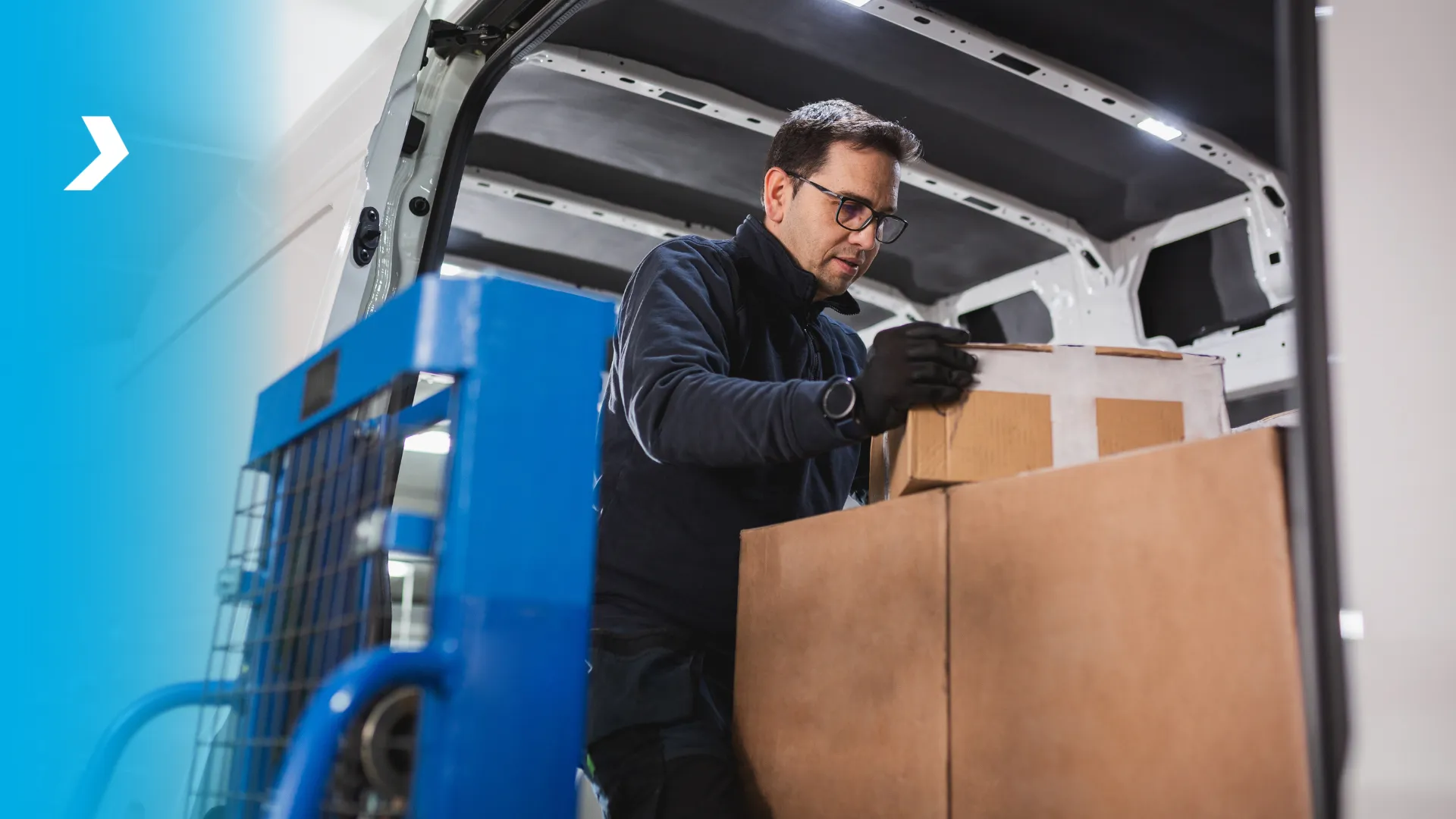
What is Reverse Logistics? The Process, Importance, and Real-world Examples
Efficient supply chain management, and reverse logistics as its integral part, is vital for businesses of all sizes and scopes striving for sustainability, cost-efficiency, and customer satisfaction. While traditional logistics primarily concerns efficiently moving products from manufacturers to consumers, reverse logistics focuses on the journey of products in the opposite direction – from consumers back to the manufacturer, seller, or distributor. With almost a trillion-dollar annual value of such returns worldwide, building a reliable and efficient reverse logistics chain has become a real game-changer in the modern supply chain landscape.
Let's delve deep into the world of reverse logistics, providing an in-depth exploration of its definition, processes, importance, and real-world examples.
What is Reverse Logistics?
Reverse logistics can be defined as the complex process of planning, implementing, and controlling the smooth flow of returned products, recyclables, or waste materials from the point of consumption to the point of origin. In contrast to forward logistics, which revolves around the seamless flow of products from manufacturers to consumers, reverse logistics tackles the complexities of handling returns, recalls, repairs, recycling, and disposal. It encompasses various scenarios, including customer returns, defective product recalls, equipment refurbishments, and recycling initiatives
The scenarios where reverse logistics comes into play are uncountable. Here are some common situations where reverse logistics works:
- Customer Returns: Any situation when customers return products because of dissatisfaction with their quality, defects, misfit, or simply changing their minds.
- Defective Product Recalls: In cases where a product is found to be defective or unsafe by the manufacturer or seller, it can be recalled to ensure consumer safety and protect the brand's reputation.
- Product Repairs and Refurbishment: Some products may be returned for repair or refurbishment (for example, under warranty). Repair or refurbishment is required in such cases to make them saleable once again.
- Recycling: Many businesses are focused on sustainability and environmental responsibility. For example, food businesses can reuse the containers they put their food in to minimize waste and reduce the ecological footprint.
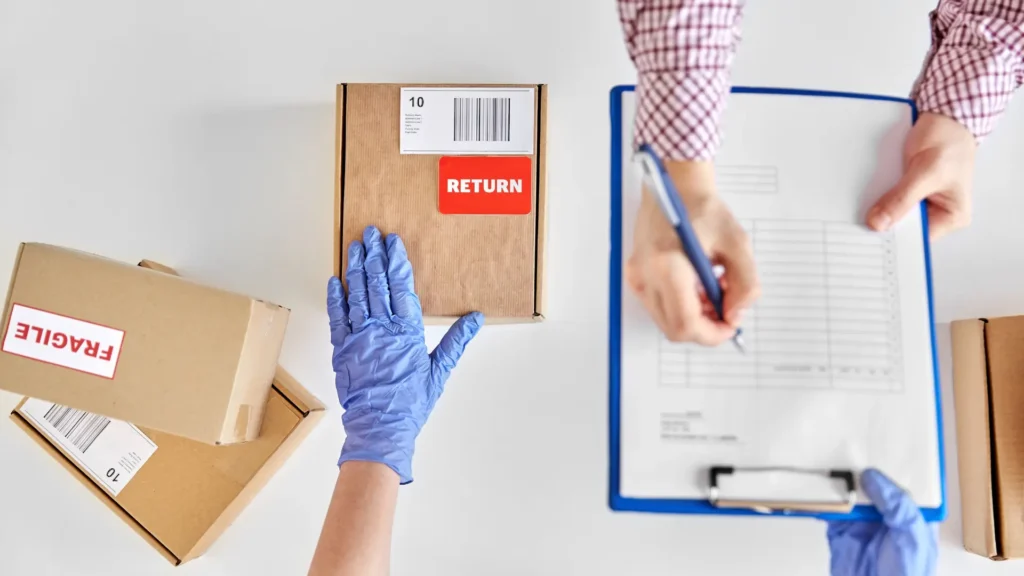
The Process of Reverse Logistics
Reverse logistics is a multi-faceted process that involves several key steps, each with its challenges:
- Product Return: Most return journeys begin when a customer decides to return a product for various reasons, ranging from dissatisfaction with the product to receiving a defective item. Picking up and managing these returns quickly and efficiently is the first critical challenge in reverse logistics.
- Inspection and Sorting: Once returned, items are carefully inspected and sorted to assess their condition. Some are ready for resale, while others may need repairs or recycling. Determining responsibility for product issues is also crucial at this stage, yet it can be challenging and may result in customer disputes.
- Refurbishment/Repair: For items that can be repaired or refurbished, this step involves the necessary actions to restore them to a saleable condition. This is a complex, costly, and resource-intensive process, requiring skilled technicians and access to replacement parts.
- Re-distribution: Once products are repaired or refurbished, they must be reintroduced into the supply chain. This can be complicated as it typically involves restocking them in inventory, sending them to secondary markets, or redistributing them to retailers or customers.
- Recycling/Disposal: Products that can't be resold or repaired usually need to be recycled or disposed of responsibly. This step can be particularly challenging due to environmental regulations and ethical considerations.
To streamline these processes, businesses employ various technologies and systems. Here are some of them:
- Advanced Tracking Systems: These systems provide real-time visibility into the movement and status of returned products, enabling businesses to make informed decisions and allocate resources efficiently.
- Automated Sorting Machines: Automated sorting systems use technologies such as barcode scanning, RFID (Radio-Frequency Identification), and computer vision to sort returned items quickly and accurately.
- Inventory Management Software: Advanced software solutions help optimize inventory management by determining which products can be repaired, refurbished, or resold and which should be recycled or disposed of.
The Importance and Real-World Examples of Reverse Logistics
Properly built and structured, reverse logistics offers a wide range of benefits, including:
- Cost Savings: By maximizing the value of returned products through repairs, refurbishment, or resale, streamlining the return process, and recycling and disposal of unsalvageable products, businesses can recover some of their initial investment while avoiding costly fines and penalties.
- Environmental Impact Reduction: By promoting recycling and responsible disposal of products and materials, companies can reduce the overall waste and environmental impact.
- Customer Satisfaction: A seamless and hassle-free return process makes customers experience ease and convenience when returning products. They are more likely to remain loyal and place new orders.
Now, let's explore some real-world examples that illustrate the importance and benefits of reverse logistics:
Imagine a major online retailer that handles thousands of customer returns each day. Here's how they can manage their product returns efficiently by optimizing reverse logistics:
- Upon receiving a returned item, the retailer's system automatically logs it, assesses its condition, and updates the inventory.
- Products deemed suitable for resale are quickly restocked in the inventory. Meanwhile, slightly damaged or refurbished items are redirected to secondary markets, where they can be sold at a reduced price.
- Products that cannot be repaired or resold are sent to recycling facilities where they are disassembled, and their components are recycled or disposed of responsibly.
This example illustrates how the retailer's investment in technology and processes pays off by reducing waste and optimizing inventory.
Now, let's consider a manufacturing company that produces electronic devices and has to recall already-sold products due to a critical safety issue. Here is a win-win plan:
- The company swiftly notifies all affected customers and retailers about the recall using an automated notification system, providing clear return instructions.
- A specialized team handles the return logistics, ensuring that the recalled items are retrieved from customers and retailers without delay.
- Upon receiving, products that can be repaired to meet safety standards are carried out promptly. Otherwise, the company provides replacements to affected customers.
- Throughout the entire process, the manufacturing company maintains transparent communication with all recall participants. Once the recall is completed, the company reports it to the appropriate authorities to build trust and credibility.
This case study demonstrates how a well-executed reverse logistics strategy can save customers, protect brand reputation, and minimize financial losses.
Conclusion
Reverse logistics is a fundamental component of a modern supply chain, addressing the crucial tasks of handling product returns, recycling, and responsible disposal. We've explored its definition, processes, and significance and provided real-life examples to understand how it can promote potential cost savings, reduce environmental impact, and enhance customer satisfaction.
While reading this, take a moment to consider how reverse logistics can be implemented or improved within your operations. By leveraging advanced tracking, sorting, and inventory systems and software, your business can unlock the benefits of well-structured reverse logistics, driving success in today's competitive marketplace.
Optimize your reverse logistics process with Expedite All, America's largest small truck network. Contact us today to streamline your operations.
You May Be Interested In
Fraud-Free Freight: Building a Resilient Transportation Network
Reliability and security are the cornerstones of every efficient business, and freight logistics is no exception. Risks like different fraudulent activities pose a severe threat, impacting financial stability, eroding trust, and compromising the efficiency of supply chains. Fraud prevention mechanisms are crucial as they prevent financial losses and maintain the integrity and reliability of transportation networks…
Mastering the Art of Sensitive Cargo Transportation
The smooth operation of industries relies heavily on an efficient supply chain, where the ground transportation industry plays one of the pivotal roles. From raw materials sourced from farms and manufacturers to the final-mile delivery, ground transportation ensures the uninterrupted…